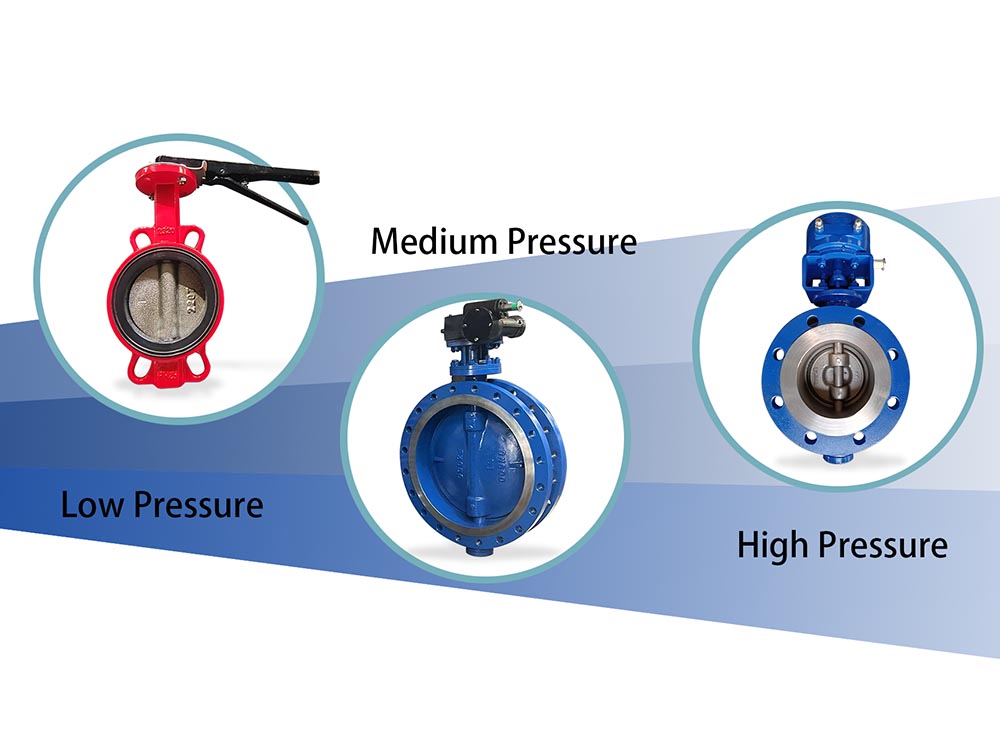
Butterfly valves are ubiquitous in industrial applications and are an important component in controlling the flow of various fluids in pipelines. A key consideration when selecting and using a butterfly valve is its maximum pressure rating. Understanding this rating is critical to ensuring safe and efficient operation of fluid systems.
In this article, we will delve into the concept of the maximum pressure rating that a butterfly valve can withstand, and study the impact on the rated pressure from aspects such as butterfly valve design, material, sealing, etc.
What is the maximum pressure?
The maximum pressure rating of a butterfly valve refers to the maximum pressure at which the butterfly valve can operate safely without malfunctioning or affecting performance. The following are several factors that determine the maximum pressure rating of a butterfly valve
1. Butterfly valve material
The materials used to manufacture the valve body, valve plate, valve stem and valve seat are the primary factors in determining the pressure rating of a butterfly valve. Materials with high tensile strength, corrosion resistance and temperature stability can withstand higher pressures. For example, stainless steel butterfly valves can withstand higher pressures due to their excellent corrosion resistance and strength.
The valve seat sealing material will also affect the pressure bearing capacity of the butterfly valve. For example, EPDM, NBR, etc. are commonly used rubber sealing materials, but their pressure-bearing capabilities are relatively limited. For applications that are required to withstand higher pressures, other more pressure-resistant sealing materials may be selected.
2. Butterfly valve structure
The structure of the butterfly valve is another important factor affecting the pressure of the butterfly valve. For example, the centerline soft-sealing butterfly valve is generally used in low-pressure systems, namely PN6-PN25. The double-eccentric butterfly valve design improves the sealing performance by changing the structure of the butterfly plate and valve seat to withstand greater pressure.
3. Butterfly valve body wall thickness
There is a proportional relationship between the size of the valve body wall thickness and the pressure. Typically the greater the pressure rating of the valve, the thicker the butterfly valve body is to accommodate the forces exerted when the fluid pressure increases.
4. Butterfly valve pressure design standards
The design standards of a butterfly valve will stipulate the maximum pressure it can withstand. Butterfly valves are manufactured in compliance with API (American Petroleum Institute), ASME (American Society of Mechanical Engineers), ISO (International Organization for Standardization) and other industry standards, and undergo strict testing and inspection to ensure that the butterfly valve meets the specified pressure level.
Are Butterfly Valves Good For High Pressure?
Butterfly valves can be divided into vacuum butterfly valves, low-pressure butterfly valves, medium-pressure butterfly valves, and high-pressure butterfly valves according to nominal pressure.
1). Vacuum butterfly valve—a butterfly valve whose working pressure is lower than standard atmospheric pressure.
2). Low pressure butterfly valve—a butterfly valve with a nominal pressure PN less than 1.6MPa.
3). Medium pressure butterfly valve—butterfly valve with nominal pressure PN 2.5~6.4MPa.
4). High-pressure butterfly valve—butterfly valve with nominal pressure PN10.0~80.0MPa.
The maximum rated pressure of a butterfly valve is just like the short plate effect of a bucket. The water capacity depends on the shortest plate. The same is true for the maximum pressure value of a butterfly valve.
So how do we determine the maximum pressure rating?
The process of determining a butterfly valve's maximum pressure rating is a series of tests performed by the manufacturer to evaluate the valve's performance and determine its pressure rating. These tests may include:
1. Material analysis
Conduct metallographic analysis on butterfly valve components to verify material properties, and conduct mechanical tests to ensure that the butterfly valve meets the prescribed standards for strength, ductility, etc.
2. Hydrostatic testing
A valve is subjected to fluid pressure in excess of its maximum rated pressure (usually at ambient or elevated temperatures) to evaluate its structural integrity and sealing performance.
1). Preparation before test
Before conducting a butterfly valve hydraulic test, the following preparations need to be made:
a) Check the integrity of the test equipment to ensure that the test can be carried out safely and normally.
b) Make sure the butterfly valve has been installed correctly and the connection with the pressure measuring machine is well sealed.
c) Select a water pump with appropriate pressure to ensure that the test pressure and flow rate meet the requirements.
d) Remove debris that may affect the test results during the test and ensure that the test environment is clean and tidy.
2). Test steps
a) First close the valve at the butterfly valve, then open the water pump, and gradually increase the water pressure to reach the test pressure.
b) Maintain the test pressure for a period of time and check whether there is leakage around the butterfly valve. If there is leakage, it needs to be dealt with in time.
c) After a period of testing, gradually reduce the water pressure and clean the butterfly valve and pressure measuring machine to avoid water stains after the test.
3). Test methods
There are mainly the following methods for butterfly valve hydraulic testing:
a) Static pressure test method: Stop the water pump, maintain the test pressure for 1-2 hours, and observe whether there is leakage around the butterfly valve.
b) Dynamic pressure test method: While maintaining the test flow and pressure, open the butterfly valve, observe whether the valve operates normally, and check whether there is leakage around it.
c) Air pressure test: Apply air or gas pressure to the butterfly valve to simulate operating conditions and evaluate its response to pressure fluctuations to ensure reliable performance under dynamic conditions.
d) Cycling test: The butterfly valve is repeatedly cycled between open and closed positions under different pressure conditions to evaluate its durability and sealing integrity.
Why determine the maximum pressure rating of a butterfly valve?
Determining the maximum pressure rating allows you to select the appropriate butterfly valve for the application and ensures safe operation within the specified pressure limits.
1. Application Compatibility
Select a butterfly valve with a pressure rating that exceeds the maximum operating pressure that may occur in the piping system to prevent overloading of the butterfly valve.
2. Temperature considerations
Consider temperature changes in the fluid system, not only due to thermal expansion and contraction. High temperatures will cause an increase in fluid pressure, and high temperatures will affect the material properties of the valve and reduce its pressure handling capability.
3. Pressure Surge Protection
Install appropriate pressure relief devices or surge suppressors to mitigate pressure surges and protect the butterfly valve from sudden pressure spikes that exceed its rated capacity.
In summary, the maximum pressure that a butterfly valve can withstand is determined by its design, material, structure, and sealing method. Maximum pressure rating is a critical parameter to ensure safe and efficient operation of butterfly valves. By understanding the factors that affect pressure ratings, how they are determined, and their impact on butterfly valve selection and use, the appropriate butterfly valve can be selected correctly to ensure the safety and performance of the butterfly valve during use.